Understanding Safety Rope Pull Switches
March 6, 2025 in Machine Safety Blog byA Comprehensive Guide for Industry Professionals
Estimated reading time: 8 minutes
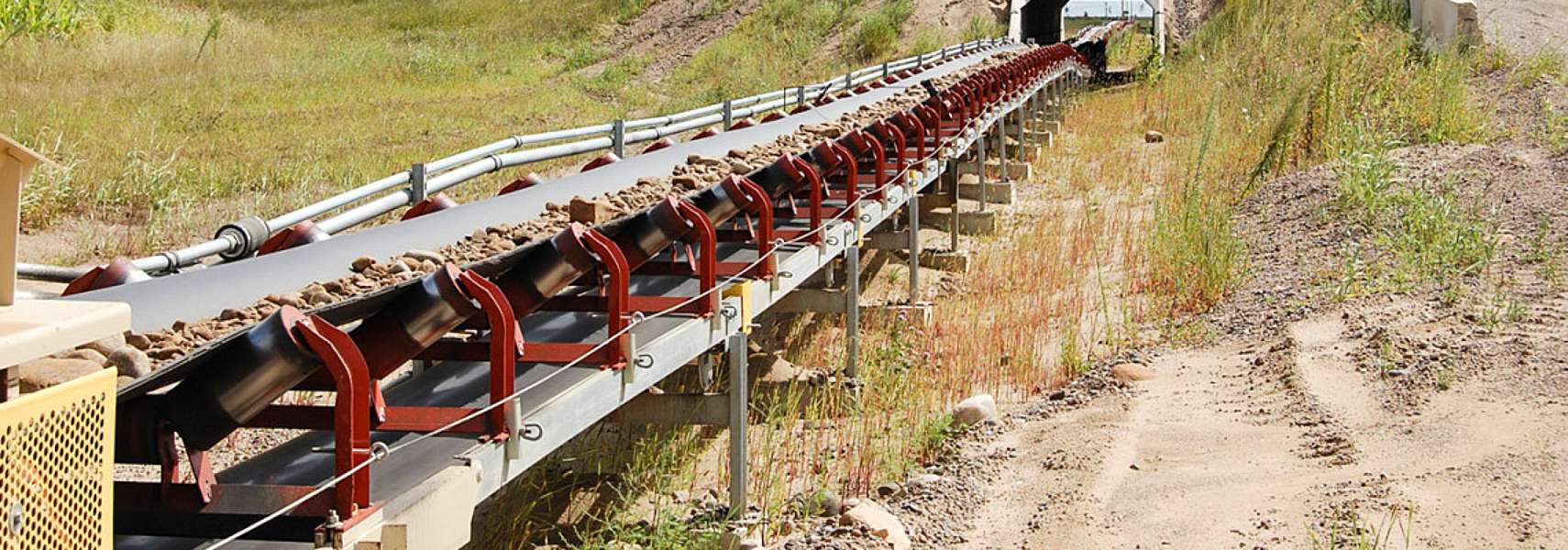
Over the years, I have visited many companies but realized I have not seen many rope pull switches installed. That could be because it was rare for me to frequent companies that used a lot of conveyor belts or large production line machinery. However, I have recommended installing rope switches for good reasons, too.
Rope pull switches, also called cable pull switches, function like emergency stop buttons but allow a machine to be stopped from any point along a designated line, making them ideal for certain applications. To demonstrate, think of pulling on a clothesline and activating a switch that turns off a light. This “clothesline” can stretch long distances and be pulled anywhere along its run.
For example, on a long conveyor belt, a fallen item, material back-up, or entanglement in the rollers may create a dangerous situation requiring quick access to a stop control. A rope safety switch allows an operator to send a stop signal by pulling the rope anywhere along its length.
Installing multiple emergency stop buttons is one way to ensure emergency stopping along a conveyor belt. However, this requires extensive wiring, increasing costs. Additionally, an operator may need to walk or run to the nearest button unless they are placed very close together. A more efficient solution is a rope safety switch, where a wire rope runs along the conveyor’s length, triggering a stop from anywhere by simply pulling the rope.
Rope pull switches are an integral part of modern industrial safety systems. Whether you’re a safety engineer, supervisor, manager, or installation technician, understanding how these devices work and how to install them effectively is key to ensuring the safety of personnel and equipment.
In this article, we’ll explain a rope safety switch’s function in everyday operations and examine some technical details that installation technicians should consider.
What Is a Safety Rope Pull Switch?
A rope safety switch is a safety device activated by pulling a rope or wire. It provides an immediate way to stop machinery in an emergency. Commonly used in industrial and mining environments, these switches integrate with emergency stop systems to help prevent accidents and injuries.
When a worker pulls on the rope, the switch activates an electrical signal that either completes or breaks a circuit. This signal typically sends a stop command to the machine, effectively halting its operation.
The rope switch by itself is useless without being connected to the rope. Thus, when I talk about installing a rope safety switch, you should assume that extra hardware is also required. In addition to the rope, you may need other items, such as:
- Rope clamps
- Wire rope thimbles
- Rope end fittings
- Turnbuckles
- Pulleys
- Wire rope guides
- Extension springs
The installer can easily purchase many items above at a local hardware store, which usually carries a variety of wire rope hardware.
How Does a Rope Safety Switch Work?
The operation of a rope safety switch is straightforward. Still, its design is a fine example of engineering simplicity meeting effective safety design. Here’s a quick breakdown of its operation:
When a worker pulls the rope in any direction, the switch is activated immediately, as the cable transmits the force from the rope switch actuator to the switch mechanism.
Notably, the switch is also built so that cutting the rope activates it as a failsafe measure. In its normal state, the wire rope is kept under specific tension to ensure that any loss of tension—such as from a cut rope—initiates the switch.
Alternatively, certain rope switches are meant to be installed in the middle of a rope run. Pulling the rope in either direction causes the switch to activate.
The rope switch activation changes the state of an electrical circuit by either completing or interrupting it, which in turn sends an immediate signal to the machinery’s control system.
Once the signal is received, the machinery is programmed to stop immediately. This is an essential feature in high-risk environments like mining or heavy manufacturing, where a swift halt can prevent serious injuries and equipment damage.
One of this mechanism’s strengths is its simplicity. It provides a reliable and effective method of ensuring safety during unforeseen incidents.
Key Benefits of Using Rope Pull Switches
For safety supervisors and managers, rope pull switches offer several benefits:
- Immediate Response: Depending on how the switch is integrated into the overall control system, it allows for an almost instantaneous equipment shutdown. This fast response time can help prevent further damage or injury in an emergency.
- Simplicity: The user-friendly design ensures that even someone with minimal technical training can operate the switch in a critical moment.
- Versatility: Rope pull switches can be installed in various settings—from manufacturing plants to mining operations—making them a versatile safety solution. Wire rope is flexible and can turn around corners with the assistance of strategically placed pulleys.
- Reliability: These switches provide a dependable safety mechanism that meets stringent industrial standards when properly maintained and installed.
Applications Across Industries
Rope pull switches find application in diverse industries, each benefiting from the reliable emergency stop function they provide.
In manufacturing, these switches are integrated into production lines that serve as emergency stop mechanisms, capable of quickly turning off machinery to prevent accidents or machine damage.
In the mining industry, where equipment is large and inherently dangerous, rope pull switches offer a dependable emergency stop solution that enhances worker safety.
In construction, heavy machinery is often equipped with these switches as part of comprehensive safety protocols, ensuring that the equipment can be halted immediately when necessary.
Additionally, automated systems frequently incorporate rope pull switches to add an extra layer of protection against system malfunctions.
Collectively, these varied applications underscore the significant role that an effective emergency stop system plays in maintaining safety across different industrial environments.
Application Example: Plate Rolling Machine
The industry uses plate rolling machines to bend flat metal sheets into curved or cylindrical shapes. These machines are commonly used to manufacture tanks, pressure vessels, snowplows, and other rounded structures.
Plate rolls range from compact units to massive industrial machines used in shipbuilding and heavy manufacturing. Operators may work on either side of the machine, making accessible safety measures essential. A rope switch is an effective way to stop the machine quickly in an emergency.
📽️ Watch how a rope switch functions on a plate rolling machine: Video Link
We’re just a Phone Call Away.
Ferndale Safety can help you with:
Fill out the form, and one of our safety experts will get in touch with you shortly.
Installation and Selection: What Technicians Need to Know
For installation technicians, correctly selecting and installing these switches is fundamental to ensuring they perform as intended.
Best Practices for Installation
- Assessment of Environment: Before installation, assess the operating environment. Consider factors like exposure to dust, moisture, and extreme temperatures. Special rope switches are available for hazardous locations.
- Electrical Compatibility: Ensure the switch’s electrical ratings match the machinery’s control system. Using a device that isn’t rated correctly can lead to malfunctions or even hazards. Ensure the switch has the correct contact configuration, especially if you connect it to a safety relay.
- Mounting and Accessibility: Install the switch in an easily accessible location. In emergencies, the user should be able to pull the rope without any hindrance. Use appropriate fixtures to secure the switch, ensuring it does not become dislodged or damaged during regular operation.
- Positioning: The switch should be mounted to avoid accidental activation while remaining within reach.
- Testing and Regular Maintenance: Once installed, test the switch periodically. Regular maintenance checks help ensure that the switch remains responsive and in good working order. Documenting these tests is good practice to meet safety compliance standards.
- Training: Equip staff with clear instructions on how to use the rope safety switch. Even though the device is designed for simplicity, proper training ensures everyone knows what to do in an emergency.
Technical Considerations for Installation Technicians
For those looking for a more detailed technical overview, here are some additional points:
- Response Time: Evaluate the switch’s response time in the context of the overall safety system. This is important when doing a safety risk assessment.
- Debounce Mechanisms: Some switches incorporate a debounce circuit to prevent false triggering from vibration or minor accidental pulls.
- Compliance with Standards: Installation technicians should be familiar with relevant industry standards and regulations. Adherence to these standards improves safety and helps avoid potential legal or compliance issues later on.
- Environmental Sealing: Depending on the installation location, the switch may need additional sealing or protection from the elements. This is particularly important in outdoor or harsh industrial settings. Especially important is checking the NEMA and IP ratings and using appropriate cable glands and
- Documentation: Keep detailed records of the installation process, including wiring diagrams and test results. This documentation is vital for future maintenance, troubleshooting, or audits.
By focusing on these technical aspects, installation technicians can help ensure that rope pull switches are installed correctly and optimized for the specific demands of their operational environment.
Conclusion
Rope pull switches are an effective and straightforward safety measure. Their simple yet effective design allows immediate action during emergencies, reducing risks and protecting personnel and machinery. For safety engineers, supervisors, and installation technicians, understanding how these switches work and how to install and maintain them is fundamental to creating a safer work environment.
Whether you’re looking to integrate a new safety system or update an existing one, keep these insights in mind. With careful planning, proper installation, and ongoing maintenance, rope pull switches can be a reliable component of your overall safety strategy.