Two-Hand Control for Machine Safeguarding
June 3, 2024 in Machine Safety Blog byEstimated reading time: 11 minutes
An adequately installed two-hand control on an operating machine will keep its operators’ hands away from dangerous areas. These hazardous areas include dangers such as crush points.
What’s a crush point?
A crush point is any location where a body part might become trapped between two moving objects or one moving towards a stationary object.
A power press die is an example of a crush point hazard. Used to shape or cut metals, the power press exerts a significant force to drive the upper die into the lower die, compressing them together. The area between the two has a severe crushing hazard.
How Does it Work?
The basic principle of operation is simple: The operator must press or hold two devices simultaneously to start the machine. If they let go, the machine stops immediately.
This type of control ensures that the machine “knows” that the operators’ hands are nowhere near any moving hazards.
However, very specific conditions must be met. Installing a two-hand control incorrectly will not reduce risk or increase operator safety.
Applications of Two-Hand Controls in Machinery
Two-hand controls are used on machines where physical safeguards are impossible to implement. These include power presses, press brakes, punch presses, and automated test benches.
When considering the installation of two-hand controls on a machine, it’s very important to address other risks, such as ejections. Two-hand controls do not prevent objects from being ejected from a machine and striking an operator. In such cases, physical safeguards are crucial.
Two-Hand Control Components
A two-hand control system has two main components:
- The two-hand control device(s): These are usually push buttons but can also be special hand sensors requiring zero activation force. There needs to be two, one for each hand. Some manufacturers offer a pre-built unit with two buttons, an enclosure to separate them, and an emergency stop button or other controls.
- Safety Control Module is a specialized piece of electrical hardware made specifically for two-hand operations. It includes a built-in timer and safety circuitry to detect faults. This safety control module is often sold as a specific type of safety relay, such as the two-hand safety control relay.
Note: Although a two-hand control device can be a sensor, pressure-sensitive device, button, etc., I will refer to it as a “button” for simplicity. Comparatively, I’ll use “safety relay” to refer to the two-hand safety control module.
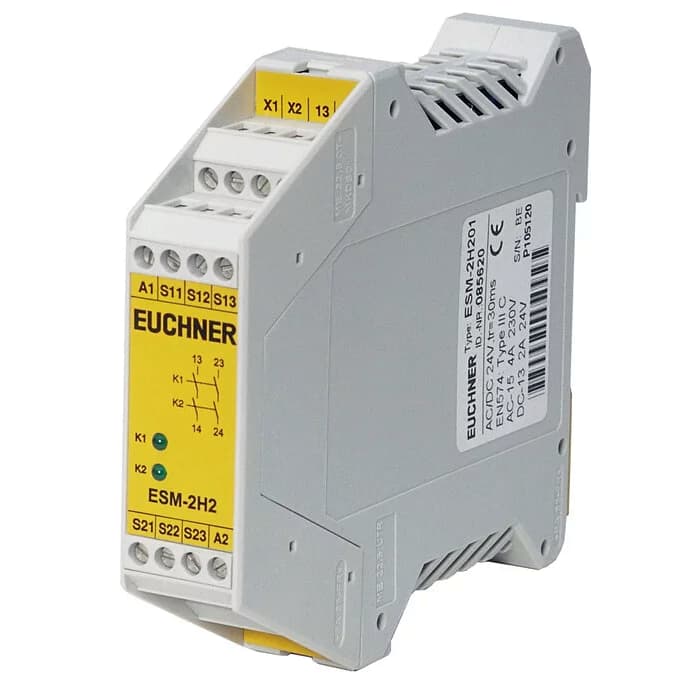
The Safety Control Relay
An example of a two-hand safety control relay. Each of the two buttons is hooked up to this safety relay, ensuring the buttons are pressed simultaneously. In addition, the safety relay verifies and checks that there are no faults or problems in the two-hand control system.
I have seen many machines with two buttons but omit the controller. This could be because the installer did not know how to install a two-hand station properly, or it could have been done intentionally to save money. The latter is problematic because cheaping out on safety ends up costing much more in the long term. I’ll get to the installation specifics of these components later in this blog post.
Both Hands Must be Used
The most important feature of two-hand controls is that both hands must be used together to start the machine. Unlike a simple start button or switch, which can be activated with one finger, a two-hand control will have two buttons placed a certain distance apart.
That seems simple enough, but it also means that you should not put the buttons so close together that you can push them both with one hand.
In other words, I could theoretically press two buttons with one hand if they are spaced 8 inches or less apart. I tested this with a wooden ruler and took a photo.
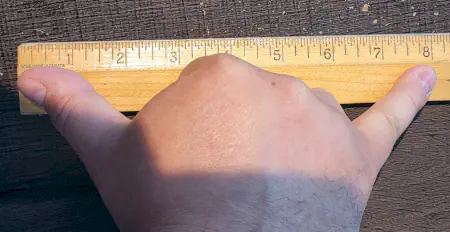
Notice how the distance between my thumb and pinky finger is enough to span 8 inches simultaneously with one hand.
OK, fine then, let’s space them further, preventing someone from using one hand. Let’s say I place them 18 inches apart; that will prevent someone from using one hand to push both buttons, right?
On the contrary, it won’t, because they could just use their arm!
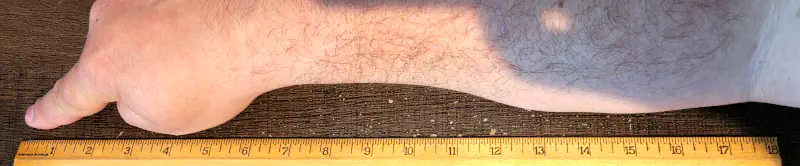
And if you think that is a bit ridiculous, consider this:
A worker is tasked with compression testing a small test piece quickly. The part is oddly shaped and won’t stay on the test bed. The worker could build a jig or holder to seat the test piece correctly.
However, human nature dictates that the worker, being pressed for time, may try to hold the piece instead. They use one hand to steady the part and push the two-hand control with their arm—elbow on one button and their pointer finger on the other.
Does it sound unlikely? Maybe. But odder things have been tried before, resulting in accidents, all in the name of cutting corners and saving time.
This is why we have specific standards. In fact, this is an actual accident in which the worker had a finger crushed in the machine. Even though the machine had a “two-hand control,” it was installed incorrectly, which did not prevent the worker from injury.
Mounting the Two Buttons
So long as we space the buttons far enough apart, an operator won’t be able to use their arm or hand to operate the machine. We don’t want to space them too far apart, but how far should they be?
Space buttons at least 24 inches apart.
Buttons should be as far apart as possible. In fact, make them at least 24 inches apart and ensure they are flush-mounted (You need to push them in with a finger instead of your palm).
I don’t recommend installing buttons inline and open because it’s just as easy for someone to push both buttons simultaneously using a wooden board, for example.
A better option is to use a special enclosure for the buttons that shroud them, like this one from Schmersal. The buttons can be closer if they are protected against unintended operation by the design, construction, and separation of the buttons [29 CFR 1910.217(b)(7)(v)(a)].
The shrouds over the buttons prevent elbow activation, and the buttons themselves don’t have to be flush mounted; they can be wider palm-style buttons for more ergonomic control.
The ½-Second Rule
Don’t replace a single start button with two buttons connected in series.
This may be a little technical for some, but it is important to know.
We don’t want to run into a situation where two buttons are installed in series to make it look like a two-hand safety device (spoiler: it’s not!).
I mean connecting one button’s output to the 2nd button’s input. Both must be pressed together to get an output from the 2nd button. However, somebody could tape down one button and semi-permanently bypass it without a safety relay.
Find Out for Yourself
I have seen many machines with two buttons, albeit without a safety relay.
Here is a simple test to verify if a proper two-hand safety relay is present and being used.
Step 1: Depress one of the two-hand controls/buttons and hold it.
Step 2: Wait 5 seconds
Step 3: Depress the 2nd two-hand control or button.
If the machine starts, it is designed incorrectly and probably does not have a two-hand safety relay.
Why is this?
The buttons must be pressed within 0.5 seconds of each other.
A two-hand control without a special safety relay will allow the machine to start in this manner because it lacks synchronous actuation enforcement, that is, enforcement of pushing both buttons at the same time. Without this enforcement, one of the buttons could be taped up or pushed in with a weight, defeating the two-hand safety feature and enabling starting the machine with only one button.
Using a two-hand control safety relay forces the user to press both buttons simultaneously within half a second of each other, preventing the user from bypassing one of the buttons.
Here is an example of what not to do when wiring up a two-hand control. This example does not have synchronous actuation enforcement.
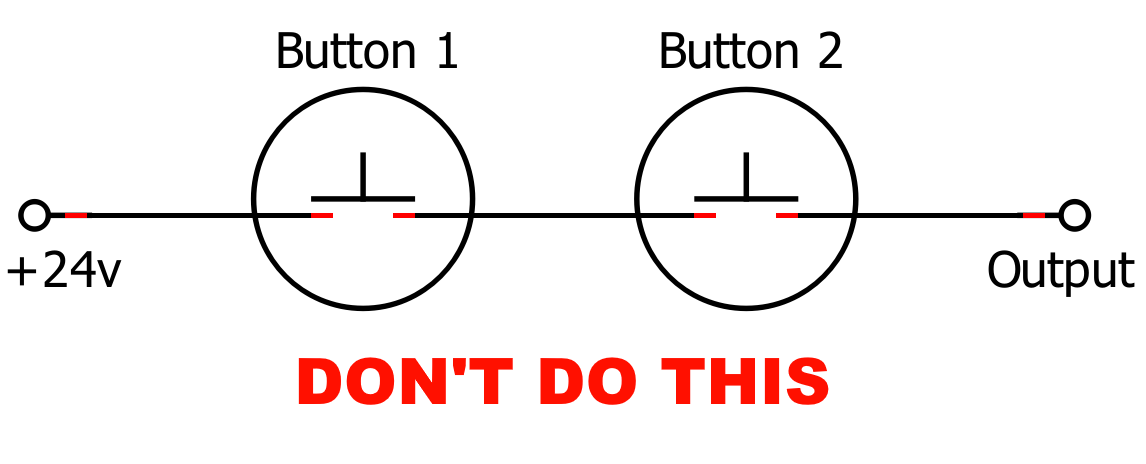
Instead, connect the buttons to a two-hand safety relay. The electrical diagram looks something like this:
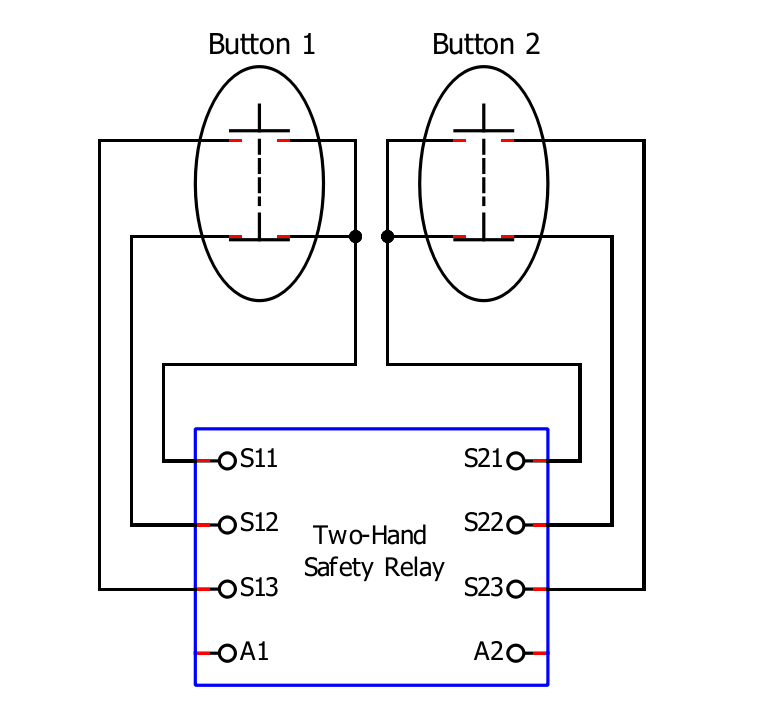
Fault Detection
A two-hand safety relay not only enforces synchronous actuation but can also detect faults such as short circuits.
Take a look at the two-hand safety relay electrical schematic above. Notice that each button has not two but three separate wires connected to it. Each button has two contacts: one normally open contact and one normally closed contact.
A single fault or a malfunction does not lead to the loss of the safety function, and every fault is detected by self-monitoring before the subsequent actuation.
If one of the contacts gets stuck, the safety relay will detect the fault the next time the button is pushed because it “sees” that only one has changed states.
The safety relay can detect faults such as:
- Open/short circuits
- Ground faults
- Cross-circuit faults
- Welded contacts
- Undervoltage/Overvoltage
- Wiring faults
- Etc.
Two-Hand Control Safety Distance Calculations
Now that we know the distance between the buttons, we need to know how far away to put them from the machine’s hazardous area.
OSHA’s Code of Federal Regulations 29 CFR 1910.217(c)(3)(vii)(c) states that “The safety distance (Ds) between each two-hand control device and the point of operation shall be greater than the distance determined by the following formula: Ds = 63 inches/second × Ts“
After releasing the two-hand control, the operator should not be able to reach an active hazardous area. We will install the two-hand control at an adequately calculated distance from the machine hazard.
Check out the safety distance calculator below. Keep the Ds value at 63 and try a different Ts parameter value, which is the machine’s stop time (Everything has stopped moving).
The calculator gives the minimum distance from the machine hazard area where the two-hand control buttons must be. Three seconds does not seem like a lot of time; in reality, a three-second machine stop time means you would have to move the two-button operator station about 16 feet away!
Want to find out more about safety distance calculations? Click here for a more in-depth article about the subject.
Conclusion
As you can see, there’s more to two-hand controls than what meets the eye. A two-hand control system should have all the following features:
- Both buttons must be pressed concurrently
- The buttons must be protected from unintended operation
- Reliability of the control system
- Mounted a safe distance from the hazard
Once correctly installed, a two-hand control system should help prevent avoidable operator injuries.
Need help?
Ferndale Safety can help you with:
Please fill out the form below so that one of our safety experts can call you. Alternatively, you can click here to send us a message.
References
EN ISO 13851, Safety of Machinery – Two-hand control devices – Principles for design and selection
EN ISO 12100 – Risk Assessment and Risk Reduction
EN 60204-1 Electrical Equipment of Machines Part 1: General Requirements
EN ISO 13849-1 Safety-Related Parts of Control Systems
EN 13855 (EN 999) The Positioning of Protective Equipment in Respect to Approach Speeds of Parts of the Human Body
OSHA 29 CFR 1910.211 – Definitions
OSHA 29 CFR 1910.212 – General requirements for all machines.
OSHA 29 CFR 1910.217, Mechanical Power Presses
Two-hand control (Part-revolution only) – 1910.217(c)(3)(viii)
ANSI B11.0 Safety of Machinery, General Requirements, and Risk Assessment
ANSI B11.19 Performance Criteria for Safeguarding
NFPA 79 Electrical Standard for Industrial Machinery
Note: Additional requirements may be required for power presses; this includes provisions for two operators, anti-repeat features, etc. Please see this link: https://www.osha.gov/etools/machine-guarding/presses/two-hand-controls
Sources of Standards & Regulations
OSHA Documents: https://www.osha.gov
American National Standards Institute (ANSI): https://www.ansi.org/
National Fire Protection Association (NFPA): https://www.nfpa.org
Document Center: https://www.document-center.com/
FAQ
A two-hand control ensures that a machine operator’s hands are outside moving machine parts. Each hand must physically push down or hold a device to start machine movement, preventing operator injuries such as amputations or crushing.
The requirements for a two-hand control include:
1) Both buttons must be pressed simultaneously
2) The buttons must be placed at the correct distance from the machine hazard
3) The buttons must be protected from accidental activation
4) The two-hand control must be made control reliable
For more information, see EN ISO 13851, Safety of Machinery – Two-hand Control Devices – Principles for Design and Selection.
The space between each two-hand control device or button should be at least 24 inches for open buttons.
The two-hand control standard is EN ISO 13851, Safety of Machinery—Two-hand control Devices—Principles for Design and Selection. It specifies the safety requirements of a two-hand control device (THCD) and the dependency of the output signal from the control actuating devices’ actuation by hand.