Safety Relays Explained: A Guide to How It Works
October 1, 2024 in Machine Safety Blog byEstimated reading time: 9 minutes
Updated April 30, 2025 – Corrections made based on feedback. Thanks to Frank at Automated Machine Technologies for the input.
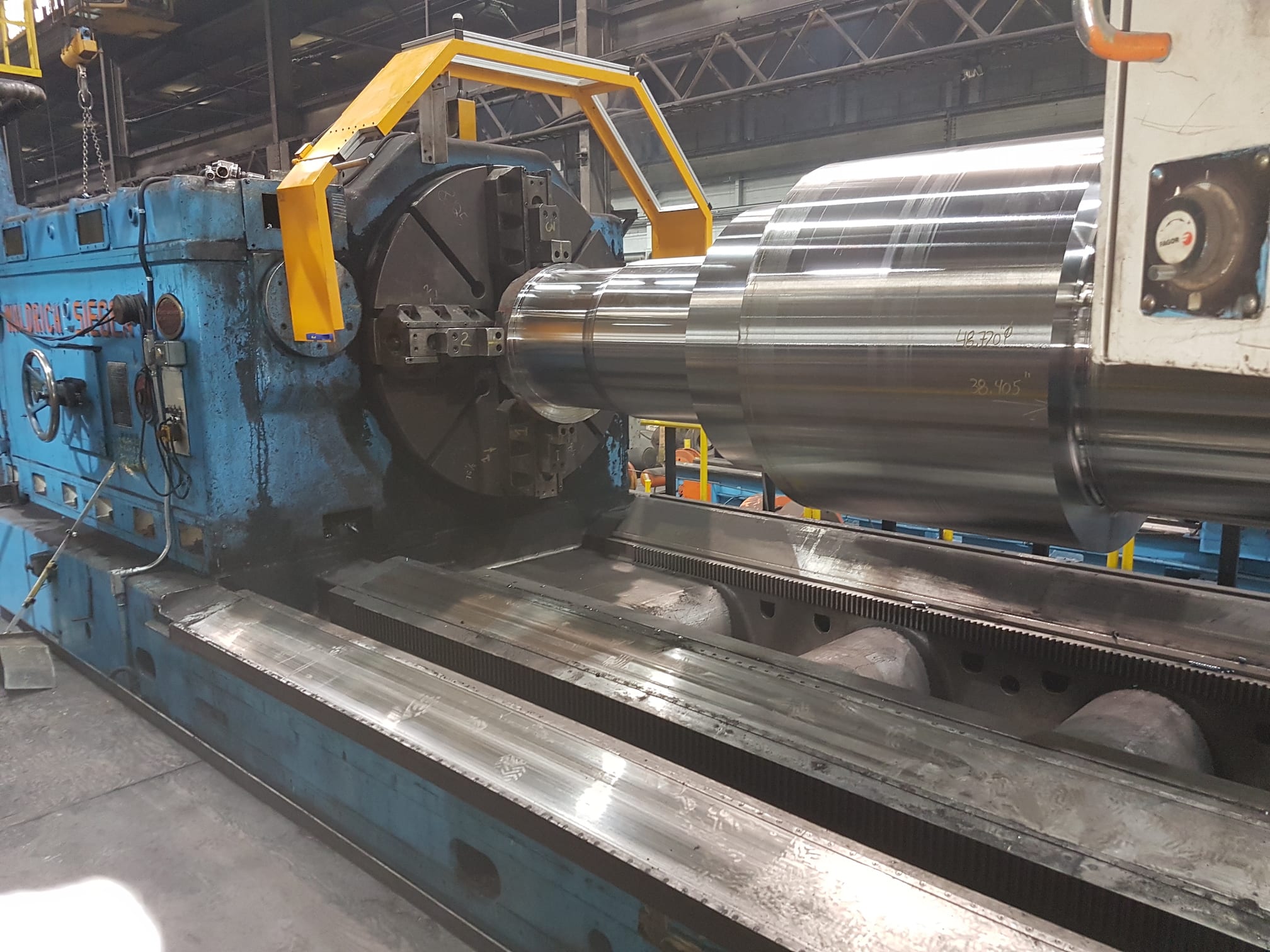
Table of contents
Introduction
A safety relay is an electromechanical or electronic device designed to reduce risk and implement safety functions, particularly in industrial environments. Its primary goal is to shut down power and remove risk safely and reliably. It reduces the risk of hazards and decreases the chance of damage, injury, or death.
It’s important to note that a safety relay is not a stand-alone device. Still, we install it as part of a more extensive control and safety circuit inside a machine. It serves as an interface between safety devices and machine components.
Unlike regular relays, we build safety relays to meet stringent safety standards, incorporating fail-safe principles that guarantee operational safety in critical conditions. A safety relay helps to check for losses in safety functions and detect internal failures, including faults with its inputs and outputs.
Safety relays are crucial in protecting workers from hazardous machinery and preventing system failures in automated systems. While installing a safety relay is not obligatory, it simplifies safety circuit design, increases the machine’s safety level, and helps detect faults.
History of the Safety Relay
The German automation manufacturer Pilz developed the first safety relay and patented the PNOZ brand emergency stop relay in 1987.
Various manufacturers now produce safety relays with a range of different functions and features. For example, a two-hand safety relay is an example of a function-specific safety relay.
Risk Assessments
You should base the safety relay and overall safety system you choose on the results of a risk assessment for the machinery.
Although I won’t cover the details here, it’s essential to understand performance levels (PL), safety categories, and Safety Integrity Level (SIL) when selecting the appropriate safety system. Suppose you connect a low-PL component to a high-PL component. In that case, the entire system will be downgraded to the lowest PL.
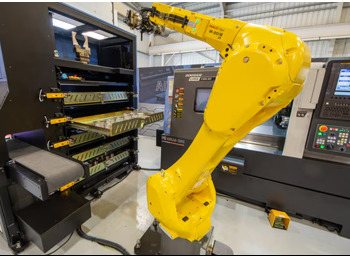
Basic Construction of a Safety Relay
A safety relay typically has several safety inputs and outputs, depending on its type. These are terminals where you can connect your wires or cables.
So, if we start on the input side, we will connect a safety device to the safety relay. An example of a device that connects to the input of a safety relay is a safety interlock switch, an emergency stop button, or a light curtain. You can even connect the outputs of one safety relay to the inputs of another safety relay. (This is a way to “daisy-chain” safety relay modules.)
An essential aspect of the safety inputs of many safety relays is that they feature dual-channel redundancy.
Dual-Channel and Redundancy
Signal redundancy ensures that a single fault on a line will not compromise the safety function. We will discuss this in more detail later, but it’s essential to wire up the safety relay correctly to maintain redundancy with these devices. You will always have two wires for each safety input on a safety relay.
Now, this is not the case for all safety circuits. Depending on the risk assessment, a single-channel device could also connect to a specific safety relay that accepts single-channel inputs. However, a single-channel safety relay would not be able to detect all the faults that a two-channel safety relay could detect.
Similarly, for the output side of a safety relay, these terminals will connect to another safety relay or a device such as a contactor. As with the inputs, the outputs are also redundant and are monitored periodically to check the status of the signals.
Usually, a compact DIN-rail-mounted unit contains all these input and output terminals. We install these units inside a machine’s control or electrical cabinet. The safety relay should also have a couple of indicator lights on its face to show its output status. Sometimes, you can diagnose a fault by seeing which indicator light of a safety input is not resetting.
Finally, the safety relay’s “brain” or internal components are a function-specific microcontroller or other circuit. It verifies and continuously checks its safety functions. Therefore, the safety relay features redundant circuits with built-in self-monitoring capabilities. If a component inside the safety relay fails, it will remain operational.
An Example Safety Relay Wiring Diagram
Here’s a fundamental example of a typical safety relay wiring diagram. Note that the wiring of the safety relay varies widely, so be sure to read your safety relay’s instruction manual carefully.
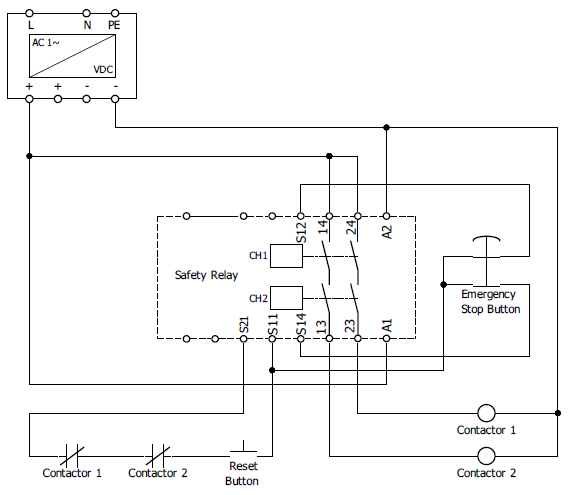
Several key points are worth noting regarding the electrical schematic above.
- Power—The safety relay and contactors are powered by a 24VDC power supply connected directly to the A1 and A2 terminals.
- The Emergency Stop Button (E-Stop)—Notice that the emergency stop button has two normally closed contacts that are mechanically connected. This is part of the redundancy-centric nature of safety systems. A pulsed signal from terminal S11 passes through both e-stop contacts before reaching terminals S12 and S14. When the E-Stop is depressed, both contacts are forced open, which cuts the signal to terminals S12 and S14.
- Safety Outputs—Terminals 14 and 24 are the input side of the safety outputs section of the safety relay. These two are connected directly to the power supply. When all safety conditions are met, the relay will close a set of force-guided* and redundant relays. This will send power to terminals 13 and 23, which will power the two contactors.
- Contactors—The safety outputs provide a dual-channel, redundant signal connected to two contactors. These contactors will then be connected in series to control a motor.
- Feedback Loop – The feedback loop monitors the contactors. In their normal state, a force-guided*, normally closed contact will inform the relay of faults within the contactor, such as welded or stuck contacts. The input for these contacts is provided by the safety relay as a pulsed signal. The two contacts are wired in series and returned to the safety relay on terminal S21.
- Reset Button—If the safety relay is tripped, this button resets the relay to its regular operation once all safety conditions are met. In this case, the signal goes through the feedback loop of the contactors.
*Force-guided: These types of contacts are designed to be mechanically connected and move together as a single unit. If a contact is stuck or welded, all other contacts will remain in their position.
What kind of faults can safety relays detect?
How Does a Safety Relay Work?
A safety relay monitors one specific safety function or a safety device, such as a light curtain. The safety relay will electronically evaluate inputs and control its outputs based on these evaluations.
Term: OSSD
OSSD Stands for Output Signal Switching Device. An electronic circuit sends out a unique pulse, recognized as a safety signal. OSSD signals prevent accidental or intentional bypassing of safety devices. The OSSD signal is not a steady 24V DC current, but rather a coded signal transmitted over a pair of wires that are out of phase with each other.
Safety Relay Functions
On a basic level, the safety relay has one or more of the following functions:
- A safety relay will still function if an internal fault is detected, allowing the system to stop or shut down due to its built-in redundancy and self-monitoring capabilities.
- The safety relay will monitor input faults, including shorts between conductors, stuck contacts, and shorts to ground.
- It has at least two inputs that receive signals from an OSSD or dry contacts, such as those found in an emergency stop button.
- A safety relay sends test pulses along its inputs and outputs to detect faults in the wires, such as shorts.
- A safety relay detects if dual-channel inputs change state simultaneously. This is to detect potentially failed contacts on an external safety device. Sometimes, a coded magnetic interlock that closes too slowly can cause the safety relay to indicate a fault because the two channels do not close simultaneously.
- It has at least two safety outputs, and many safety relays have more than two. These safety outputs use positively guided contacts to ensure that the contact sets move as a single unit.
- It allows for monitoring of output devices such as contactors. This is known as EDM, or External Device Monitoring.
- To restore a safety relay to normal operating condition after a fault has occurred, it must be power cycled or reset.
- A safety relay may have a built-in time delay or other functions such as speed or frequency monitoring.
- It provides electrical isolation between the safety devices and the power control circuit.
Proper Wiring is Important!
One crucial consideration is that for a safety relay to function as expected and reduce risk, it must be wired correctly. I have seen interlock switches wired to a safety relay’s A1/A2 power input terminals, effectively removing and deactivating power to the device. Not only is this the wrong way to connect a safety relay, but it also effectively bypasses the safety relay, making it useless in the circuit.
A typical use of a safety relay is to interconnect a safety interlock switch mounted on a guard with the contactors that power a motor.
The safety relay checks and turns on the motor contactors when all safety conditions are met.
Typical Applications & Usage Examples
We commonly find safety relays in industrial environments on machinery such as production lines, robots, and other devices where a higher safety level and risk reduction are required.
Here are examples of standard safety devices that we can connect to the input terminals of a safety relay:
- Light curtains
- Safety Mats
- Two-hand button control
- Safety guarding interlocks
- Emergency stop buttons
On the output side of a safety relay, a standard connection is made to contactors, which, in turn, connect back to the safety relay’s inputs for monitoring the contactor’s electrical contacts. In addition to contactors, we can connect a second safety relay, or we can connect to special OSSD inputs of VFDs or drives.
Examples of machinery and equipment that make use of safety relays:
- Elevators
- Cranes
- Robots
- Stamping Presses
- Cutting Machines
- Printing Machinery
- Production Machinery
Relevant Standards
OSHA 1910.211(d)(62) – Safety system means the integrated total system, including the pertinent elements of the press, the controls, the safeguarding and any required supplemental safeguarding, and their interfaces with the operator, and the environment, designed, constructed and arranged to operate together as a unit, such that a single failure or single operating error will not cause injury to personnel due to the point of operation hazards.
ANSI B11.19 & ANSI B11.20 – Control Reliability
Further Reading
https://www.ferndalesafety.com/connecting-safety-interlock-switches-in-series/
https://www.ferndalesafety.com/two-hand-control-for-machine-safeguarding/
Practical Machinery Safety By David Macdonald
Your Next Step is Just a Call Away.
Ferndale Safety can help you with:
Fill out the form, and one of our safety experts will get in touch with you shortly.