Safeguarding Plate Rolling Machines
April 9, 2025 in Machine Safety Blog byEstimated reading time: 6 minutes
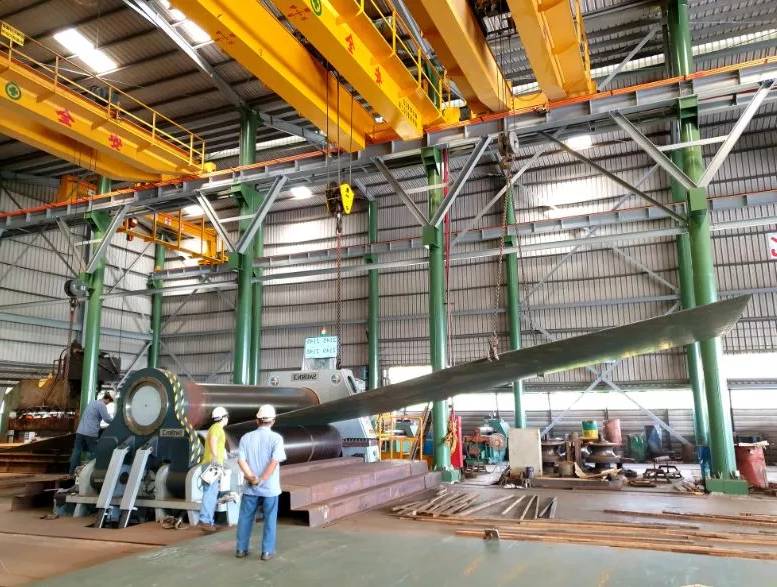
Plate rolling machines, also known as three-roll bending machines, form curves on flat stock, such as sheet metal and plate stock.
The infeed area of a plate rolling machine is one of the most hazardous zones on the shop floor. Suppose a worker gets caught between the counter-rotating rolls. In that case, the consequences can be severe — including crushing injuries, amputations, or even death. In-running nip point hazards are relatively easy to safeguard on certain machinery, but on plate rolls, it can become difficult, if not impossible.
Unlike flexible materials like paper or rubber that wrap around rollers, plate stock feeds directly into the gap between the rollers. Sheet metal or plate stock is manually inserted between the rollers. The way that the plate stock is fed into the rollers makes a nip guard safety device impractical. As the material feeds between the rollers, it can jump, and the feeding angle can change.
I would also emphasize that the material is usually not fed gingerly into the rollers. The weight of the plate stock can be measured in hundreds of pounds and is often moved with overhead cranes. Needless to say, the plate will bang up against any guarding, potentially destroying it.
The risk is exceptionally high during the initial feeding of the material when hands are closest to the rolls. Wearing gloves with exposed fingertips or loose-fitting clothing can increase the chance of getting pulled in. That’s why it’s so important to follow best practices and use proper safeguarding whenever the machine is running.
Plate rolling machine hazards
- Infeed nip point between the rollers
- Cuts & lacerations on sharp edges
- Slips, trips, and falls
- Noise
- Vibration
Let’s examine a couple of safeguarding solutions that can be made to create a safer machine.
Add a Safety Rope and Switch
Rope pull switches, also called cable pull switches, function like emergency stop buttons but allow a machine to be stopped from any point along a designated line, making them ideal for plate rolling machines. To demonstrate, think of pulling on a clothesline and activating a switch that turns off a light. This “clothesline” can stretch long distances and be pulled anywhere along its run.
The safety rope can be installed to run around corners using pulleys. Therefore, one rope pull switch can safeguard all sides of the plate roll machine.
One of the ways we can safeguard a plate roll machine is by adding a rope pull switch kit. In an emergency, the operator could pull or push the rope to signal the machine to stop immediately. Here’s a video that demonstrates how it works:
Three-Position Safety Pedals
Human instinct and behavior can often be predictable, especially in terms of basic biological and neurological reactions. For example, reflexes like pulling your hand away from a hot surface are nearly universal.
When operators are caught in a dangerous situation—like being pulled into the rollers of a plate roll machine- their response is almost always instinctive. When an operator is drawn into a plate roll machine, the instinctive response is to pull back or resist. The operator will plant their dominant foot harder for leverage to escape the danger. We can use this human reflex as a safeguard rather than a liability.
A well-designed three-position safety pedal takes advantage of this instinct. A three-position safety pedal, as its name implies, has three positions:
Position 1: Resting position; fully released
Position 2: Run position; partially pressed
Position 3: Emergency position; fully pressed
During regular operation, the operator holds the pedal in a “run” position—neither fully pressed nor fully released. If they lift their foot (intentionally or due to a fall or loss of consciousness), the machine stops. More importantly, if they press down hard—as they would when trying to pull themselves away from danger—the pedal trips the emergency stop.
This design doesn’t rely on the operator remembering a protocol or reaching for a stop button in a high-stress moment. Instead, it builds safety into what the operator’s body will do. By aligning the emergency mechanism with natural human behavior, we create a smarter, faster, and more reliable layer of protection.
Other Safeguards
In addition to the safety measures detailed above, other safeguards should be present.
- Emergency stop button: Some people may argue that emergency stop buttons are unnecessary on every machine, pointing to safety standards. In my opinion, they should be installed on every machine. A proper emergency stop button with a yellow background should be universally understood as a way to turn off a machine, allowing a bystander to shut off a machine in an emergency. An emergency stop should be installed on both sides of the rollers.
- PPE: Ensure proper PPE, such as eyewear and hearing protection, is supplied to operators. Do not use standard gloves, as they pose a drawing-in hazard.
- Environmental: Keep the area surrounding the machine clear of any tripping hazards. Ensure that the floor is not slippery. Add rubber mats to improve ergonomics.
- Electrical: Ensure you have a lock-out-tag-out procedure and a way to isolate energy from the machine.
- Training: Proper operating is essential. Operators must know how to use the machine and obey proper procedures safely. For example, standing underneath suspended plates must be strictly prohibited.
Your Next Step is Just a Call Away.
Ferndale Safety can help you with:
Fill out the form, and one of our safety experts will get in touch with you shortly.
Learn More About Machine-Specific Safety
We have more articles that may interest you on safeguarding specific types of machinery.
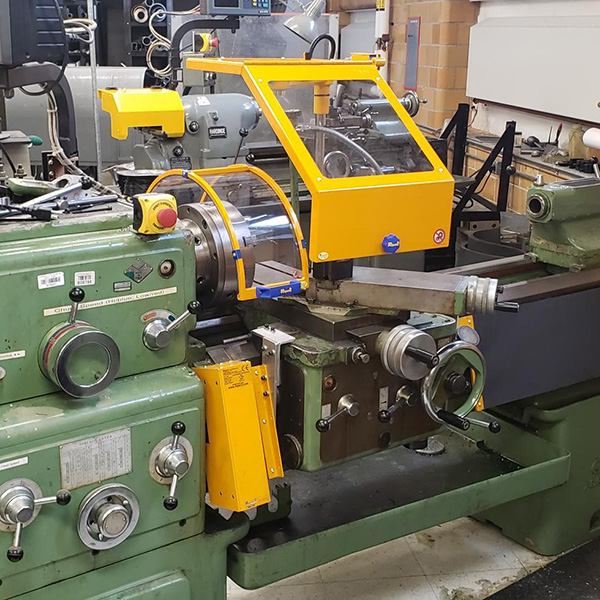
Featured Post
Find out how a lathe works and what can be done to increase lathe operator safety.
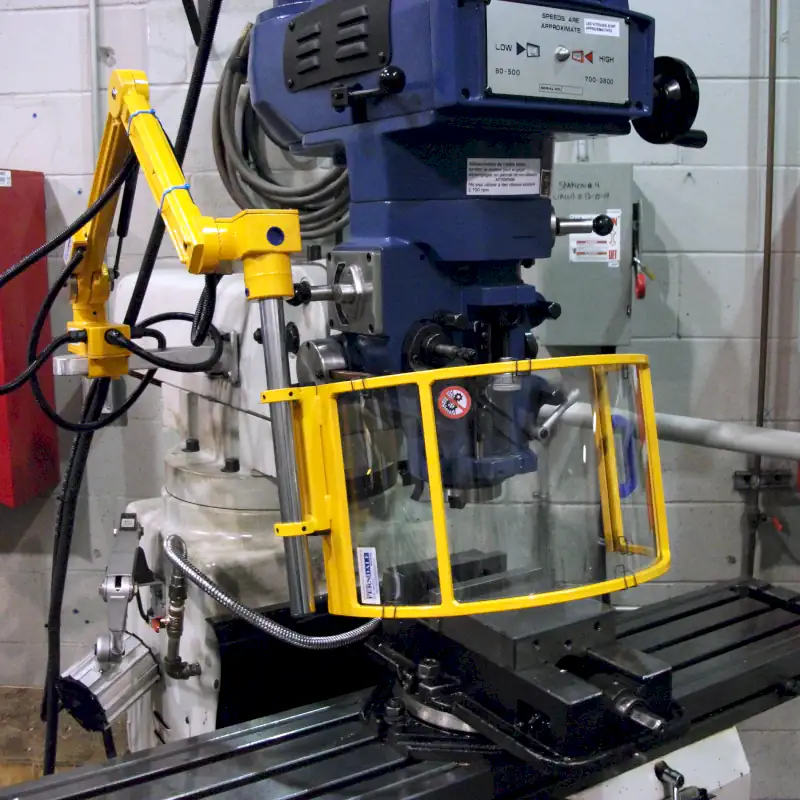
Learn about milling machines and how to safeguard them properly.
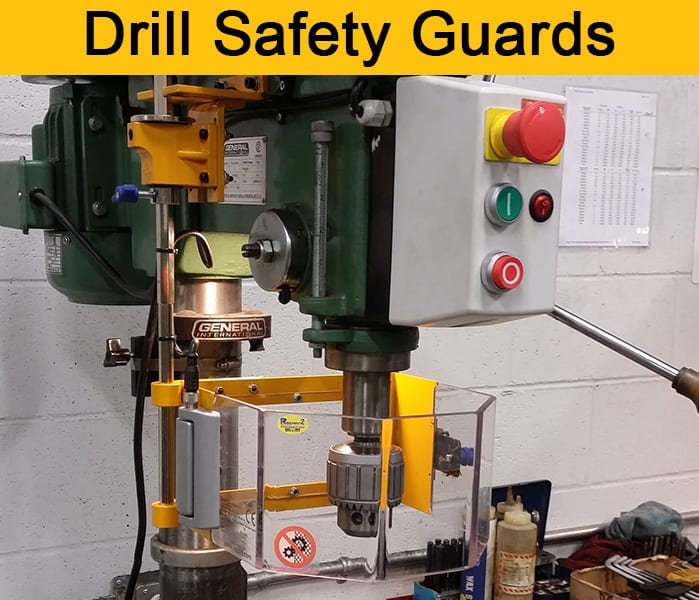
There is more to drill presses than you may think!
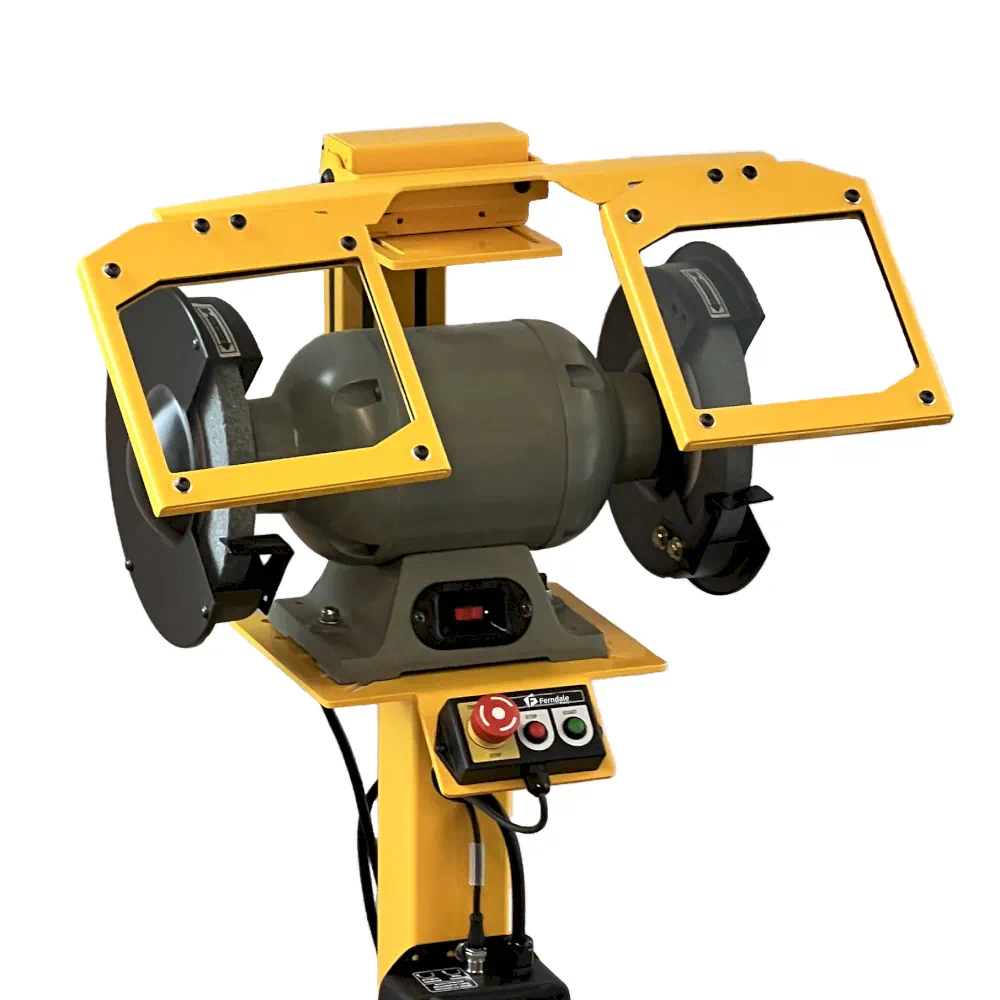
Did you know you should put anti-restart protection on your grinder?