Mechanical Hazards and Injuries in the Workplace
September 5, 2024 in Machine Safety Blog byEstimated reading time: 10 minutes
The primary purpose of machine guarding is to protect people from mechanical hazards in the workplace. However, to safeguard a machine, you should first be able to identify the primary hazards that can be found in and around machinery.
But first, let’s define mechanical hazards, and later, we will give examples.
Mechanical Hazards
“Mechanical hazard” is a general designation for all physical factors that can cause injury resulting from the mechanical action of products, processes, or services, including machinery, machine parts, tools, workplaces, and loads or from projected solid or fluid materials.
Machines can be dangerous and create hazards for the operator and others in the work area. Hazards include but are not limited to getting pulled into rotating parts, getting burned on hot surfaces, and flying debris.
These hazards can be eliminated or reduced by installing a safety guard.
Any machine part, function, or process which may cause injury must be safeguarded.
Common Mechanical Hazard Injuries
Let’s examine the kinds of injuries that can occur around operational machinery. We should have a basic understanding of these injuries to know how to protect our most important asset, people.
These are the basic injuries from mechanical hazards.
List of Mechanical Hazards
An entanglement hazard occurs when a person’s clothing, hair, or body parts become caught in moving machinery or equipment. This can result in severe injuries like crushing, cuts, or amputations. Such hazards are commonly found in industries with rotating parts, belts, chains, or gears, and they require safety measures like guards and proper clothing to prevent accidents.
An example of an entanglement hazard is the lead screw on a lathe. Many believe that there is no risk with these; however, I regularly hear about workers’ clothing getting pulled into lead screws all across the country.
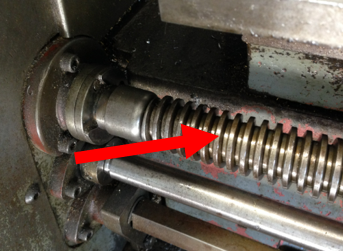
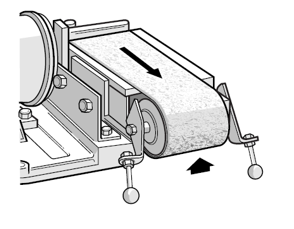
Friction and abrasion hazards arise when skin or other body parts come into contact with rough or moving surfaces, causing injuries such as scrapes, blisters, or burns. These hazards are often found in environments with conveyor belts, rotating parts, or rough surfaces. Continuous contact with these surfaces can wear down the skin or cause heat buildup, leading to abrasions or friction burns. Protective gear, such as gloves or padding, can help reduce the risk of these injuries.
Sources of this hazard to watch out for are machines such as belt sanders that use abrasive media.
Cutting or severing hazards involve the risk of injury from sharp objects or machinery with blades, such as saws or knives. These hazards can lead to cuts, deep lacerations, or the complete severing of body parts like fingers or hands.
These injuries are common in industries such as manufacturing, construction, and food processing. They are typically caused by contact with sharp edges or moving blades. Safety measures such as machine guards, proper handling procedures, and protective equipment like gloves are essential to mitigate these risks.
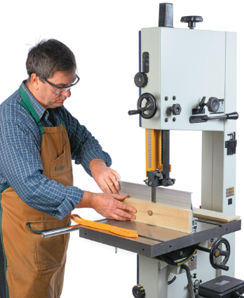
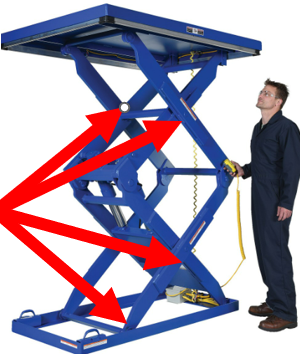
Shearing hazards occur when two mechanical parts move closely past each other in opposite directions, creating a cutting or slicing effect. These hazards can result in severe injuries like lacerations, amputations, or crushing, especially when body parts like hands or fingers are caught between the moving edges.
Shearing hazards are common in machines like metal shears, press brakes, and other cutting or shaping equipment. Safety measures, such as machine guards, proper training, and safety protocols, are critical to prevent these injuries.
Stabbing or puncturing hazards involve the risk of injury from sharp, pointed objects or tools that can penetrate the skin or body. These hazards can result in deep wounds, punctures, or internal injuries.
Common sources include nails, needles, sharp tools, or machinery parts like drill bits or spikes. If severe, these injuries can lead to infection or damage to internal organs. Safety precautions such as using protective gear (gloves, shields) and handling sharp objects carefully are essential to prevent stabbing or puncturing injuries.
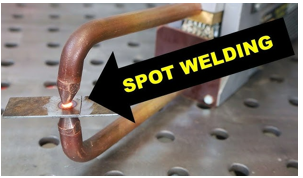
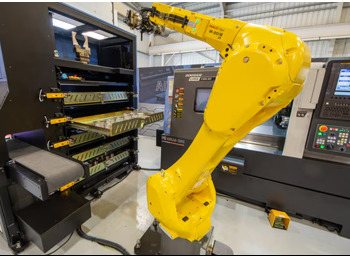
Impact hazards involve the risk of injury from being struck by or colliding with an object. This can happen when heavy, fast-moving, or falling objects hit a person or when a person collides with a stationary object. Injuries from impact hazards can include bruises, fractures, concussions, or internal damage.
Common sources include tools, machinery, vehicles, or materials being moved. Wearing hard hats, using barriers, and ensuring safe work practices can help reduce the risk of impact injuries.
Nip point hazards (pinch points) occur where two rotating or moving parts come together or a rotating part meets a stationary object. These hazards can trap or pinch body parts, such as fingers, hands, or clothing, leading to injuries like crushing, amputations, or fractures.
Nip points are commonly found in machinery with gears, belts, rollers, or pulleys. Proper machinery guarding, safe work practices, and awareness of dangerous areas around equipment are essential to reduce the risk of injury.
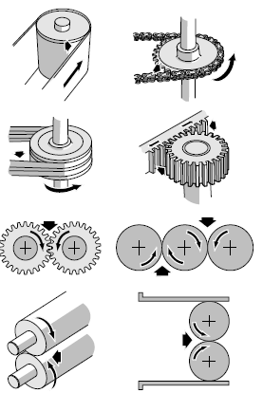
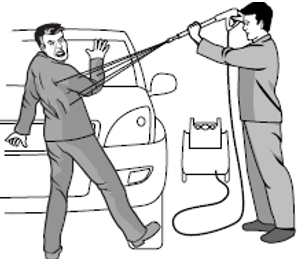
Liquid injection hazards occur when high-pressure fluids are accidentally injected into the skin or body. This can happen when working with equipment like hydraulic systems, paint sprayers, or pressure washers, where leaks or ruptures can force liquid through the skin.
Even though the injection point may appear small, these injuries can lead to severe internal damage, infection, or tissue death as the liquid spreads beneath the skin. Immediate medical attention is often required. Proper maintenance of high-pressure equipment, wearing protective gear, and avoiding exposure to pressurized fluids are essential safety measures.
Crushing hazards occur when a body part is caught between two heavy or moving objects or when a person is struck by a large object, resulting in the body being compressed or crushed.
These hazards are common in environments with machinery, vehicles, or falling objects. They can lead to severe injuries like broken bones, internal organ damage, or amputations.
Examples include being caught between a machine’s moving parts, in a vehicle accident, or under heavy equipment. Safety measures include using machine guards, following safe operating procedures, and wearing proper protective gear.
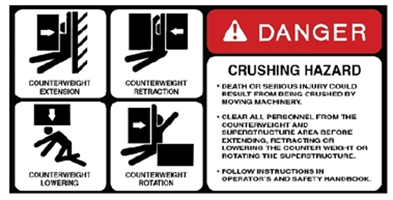
Prevention of Mechanical Hazards
Preventing mechanical hazards requires a combination of engineering controls, worker training, and consistent use of protective measures. Installing machine guards is one of the most effective ways to reduce these risks. These barriers prevent direct contact with dangerous parts like rotating gears, nip points, and cutting edges. For example, machines with moving belts or exposed blades should have guards to protect operators.
Additionally, regular maintenance is essential to ensure equipment functions correctly and avoid malfunctions that could lead to accidents. Broken or poorly maintained machinery can increase the risk of injuries like crushing or cutting.
Another critical prevention method is implementing lockout/tagout (LOTO) procedures. LOTO ensures that machines are fully powered off and cannot accidentally restart during maintenance, protecting workers from unexpected activation.
Alongside these procedures, emergency stop controls should be installed in easily accessible locations. These controls allow workers to shut down a machine quickly in case of danger.
Worker training and awareness are vital components in preventing mechanical hazards. Training programs should focus on safe operating procedures, hazard recognition, and emergency responses. For instance, if your workplace environment uses hydraulic equipment, workers must understand the risks of liquid injection hazards and the importance of handling pressurized systems cautiously.
Personal protective equipment (PPE), such as gloves, safety goggles, and steel-toed boots, is another key defense against mechanical hazards. Workers using cutting machinery should wear cut-resistant gloves. In contrast, those in environments with heavy objects should wear steel-toed boots to protect against crushing hazards. In addition, warning signs and safety labels should be placed on machinery to alert workers to specific risks and operating instructions.
Restricting access to dangerous machinery is another vital safety practice, ensuring only trained and authorized personnel operate high-risk equipment. In busy work environments, good housekeeping—such as keeping floors free of clutter—can prevent slips and falls that could result in injuries around machinery. Further, safety devices like pressure-sensitive mats or light curtains can automatically shut down machines if someone enters a hazardous area, adding another layer of protection.
Lastly, appropriate clothing and hair restraint is necessary to avoid entanglement hazards, where loose clothing or long hair could get caught in moving machinery. By combining these preventive measures—machine guards, regular maintenance, lockout/tagout procedures, proper PPE, and ongoing worker education—workplaces can significantly reduce the risk of injury from mechanical hazards, creating a safer and more efficient environment.
Schedule a call with us today.
Ferndale Safety can help you with:
Please fill out the form below so that one of our safety experts can call you. Alternatively, you can click here to send us a message.